Formenbauer sollen die Formenplanung sorgfältig und streng nach den obengenannten Referenzen und Anforderungen des Kunden durchführen. Während des Entwurfsverfahrens sollen jede Anforderung in spezifische technische Details übersetzt und in Form von Zeichnungen oder technischen Dokumenten dargestellt werden. Der Entwurfsvorgang folgt im Allgemeinen den folgenden Schritten:
1. Analyse und Verständnis von Kunststoffproduktzeichnungen und physikalischen Proben
Vor dem Formenentwurf ist eine detaillierte Analyse und ein umfassendes Verständnis der Produktzeichnungen oder physikalischen Proben unerlässlich. Die Analyse umfasst die folgenden Aspekte:
(1) Geometrische Konfiguration des Produkts;
(2) Maße, Toleranzen und Design-Referenzpunkte;
(3) Technische Spezifikationen (d. h. Leistungsanforderungen);
(4) Name und Grad des Kunststoffmaterials;
(5) Anforderungen an die Oberflächenfinishierung.
2.Bestimmung der Spritzgießmaschinenmarke
Die Auswahl der Spezifikationen der Spritzgießmaschine basiert hauptsächlich auf der Größe des Produkts und der Produktionsmenge. Designer sollen die folgenden Parameter berücksichtigen:Injektionsvermögen, Klammpresse und Modell-Umsatzrate;
(1) Effektive Formenmontagefläche (Abstand zwischen Zugstäben);
(2) Formendicken-Toleranz, Typ des Austriebsmechanismus und Hublänge.Wenn der Kunde eine bestimmte Maschinemarke angegeben hat, müssen Designer ihre Parameter prüfen. Wenn die Anforderungen nicht erfüllt sind, ist eine Beratung mit dem Kunden zur Austausch der Maschine notwendig.
Bestimmung der Werkzeugkammermenge und Anordnung
3. Die Anzahl der Werkzeugkammern wird durch Faktoren wie folgt bestimmt:
(1) Produktgewicht vs. Maschineneinspritzvermögen;
(2) Projektierte Fläche vs. Klammpresse;
(3) Formendimensionen vs. Maschinennutzungsraum;
(4) Anforderungen an die Abmessungsgenauigkeit;
(5) Farbkonsequenz;
(6) Vorhandensein von Seitenkernen und Austriebsmethoden;
(7) Produktionsmenge (monatliche/jährliche Chargen);
(8) Wirtschaftlichkeit (Produktionskosten pro Zyklus). Diese Faktoren können in Konflikt stehen und erfordern eine Abwägung.,um kritische Anforderungen priorisieren.Nachdem die Anzahl der Werkzeugkammern bestimmt ist, muss ihre Anordnung die Formendimensionen, die Balance des Zuführsystems, die Kernziehungsmekanismen und die Wärmewirtschaft optimieren. Anpassungen sind oft nötig, um sich an die Entscheidung über die Trennfläche und den Torspalt zu koordinieren.
4.Bestimmung der Trennfläche
Die Trennfläche, die manchmal in ausländischen Produktzeichnungen vorgegeben ist, wird oft von Designern bestimmt. Die wichtigsten Prinzipien sind:
(1) Vermeiden von Einflüssen auf die Ästhetik des Produkts, insbesondere für Bereiche, die für das Erscheinungsbild kritisch sind;
(2) Gewährleistung der Abmessungsgenauigkeit;
(3) Erleichterung des Formenherstellung, insbesondere der Werkzeugkammerbearbeitung;
(4) Optimierung des Zuführ-, Entlüftungs- und Kühlsystems;
(5) Gewährleistung eines zuverlässigen Austriebs, vorzugsweise das Halten des Produkts auf der beweglichen Form;
(6) Vereinfachung der Montage von Metalleinlagen.
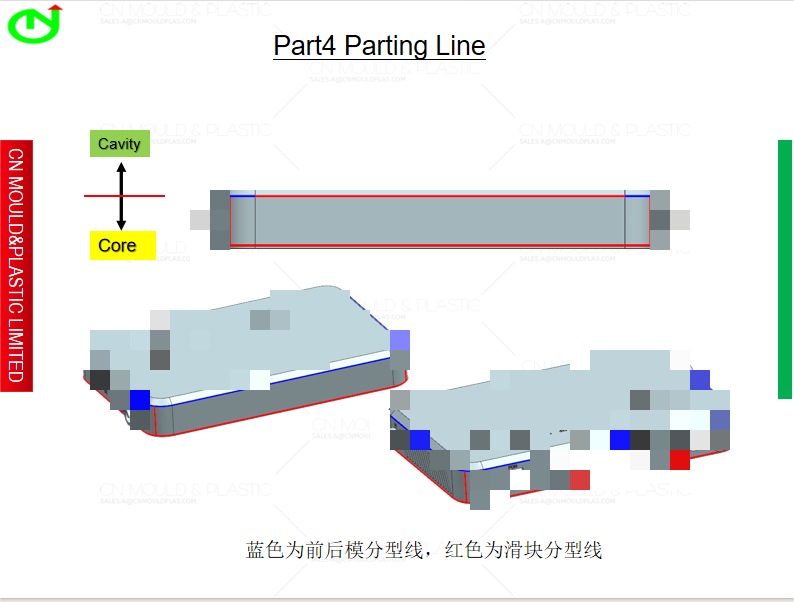
5.Entwurf des seitlichen Trenn- und Kernzie Mechanismus
Seitliche Mechanismen müssen stabil sein und eine Störung des Austriebssystems vermeiden. Wenn eine Störung unvermeidbar ist, muss ein Vor-Austriebs-Rücksetzungsmechanismus eingebaut werden.
6.Entwurf des Zuführsystems
Das Entwurfs des Zuführsystems umfasst:Auswahl des Hauptlaufs, Querschnittsgeometrie und Abmessungen des Laufs, Torspaltposition, -typ und Querschnittsgröße.Bei Punktgassen ist ein Gassendemontage-Mechanismus erforderlich, um den Austrieb des Laufs zu gewährleisten. Die Auswahl der Torspaltposition folgt diesen Prinzipien:
(1) Positionieren der Gassen auf der Trennfläche für leichte Reinigung;
(2) Minimieren der Strömungsbahnenlänge und Gewährleisten einer einheitlichen Füllung;
(3) Direktes Ziehen der Schmelzeströmung zu dickwandigen Bereichen;
(4) Vermeiden eines direkten Auftreffens auf Kerne, Einlagen oder Werkzeugkammerwände, um Verformungen zu vermeiden;
(5) Minimieren von Schweißlinien oder Positionieren in nichtkritischen Bereichen;
(6) Förderung der parallelen Strömung und effizienten Entlüftung;
(7) Plazieren der Gassen an leicht abschneidbaren Stellen, ohne die Ästhetik zu beeinträchtigen.